THUNDER is a multi-disciplinary low-technology readiness level (TRL) 24-month proposal perfectly aligned with the HFRI’s funding policy of basic research, especially that of ThA1/ scientific field 1.11 aiming to deliver: “Unique architectures, high performance, lightweight and low-cost all polymer three-dimensional printed (3DP) soft actuator devices based on new materials with electrothermal- Joule heating property, exhibiting temperature- (T) responsive behavior towards 4D-printed (4DP) components, being the key in modern high-end applications, e.g. soft robotics, biomedical, etc. products (Fig. 1) [1] [2].
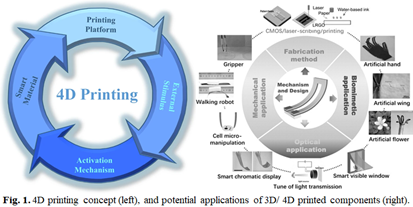
4DP materials are an emerging field of research, because the physical 3DP object’s structure can change shape (from 3D to “4D”) with response to an external stimulus, e.g. temperature, pH, light, electric, field, etc.
In specific, there are several studies reported to date in the field of 3DP/ 4DP using polymer-based (soft) materials with a shape memory effect (SME)1 4 5. Thermal energy is acquired by heating the polymer chains above the glass transition temperature (Tg), which allows the 3DP components to change their shape reversibly (Fig. 2a)1 [3] [4]
To that end, there have also been reported 4DP structures based on soft electroactive materials (e.g. electrorestrictive, electrocapacitive) with simple or more complex architectures. Such 4DP components could be “programmable” soft electrothermal actuators (ETAs) for various potential applications e.g., robotics, artificial muscles, etc. representatively shown in Fig. 2b[5].
For both cases of thermally activated soft actuators shown in Fig. 2, the main mechanism of actuation, arises from a thermomechanical strain-induced field achieved via the utilisation of two polymers with significantly different coefficient of thermal expansion and moduli, so that they could expand at different rates as they are heated up[6] [7]. Such 4DP stimuli-responsive materials and structures play a key role in designing soft robotics thanks to their brilliant shape recovery properties under applied stimuli that help the creation of programmable and accurate motion.
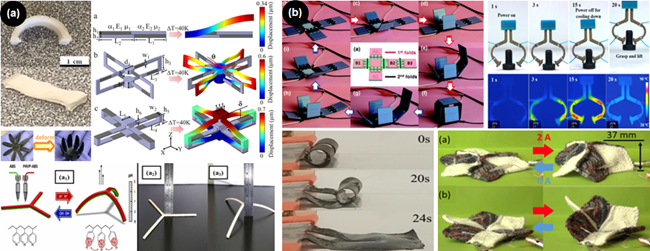
Fig. 2. 4DP components towards 4D “programmable” geometries based on: (a) temperature-responsive polymers and application of an external temperature variation, and (b) electroactive- electrothermal Joule-heating polymers by the application of an external direct-current (DC) voltage bias (Vbias).
“Acknowledgement for Funding”
THUNDER research project received funding from the Hellenic Foundation for Research and Innovation (HFRI) under the HFRI Greece 2.0 Basic Research Financing Action (Horizontal support of all Sciences) Sub-action II Funding Projects in Leading-Edge Sectors (Project ID Number: 15515).
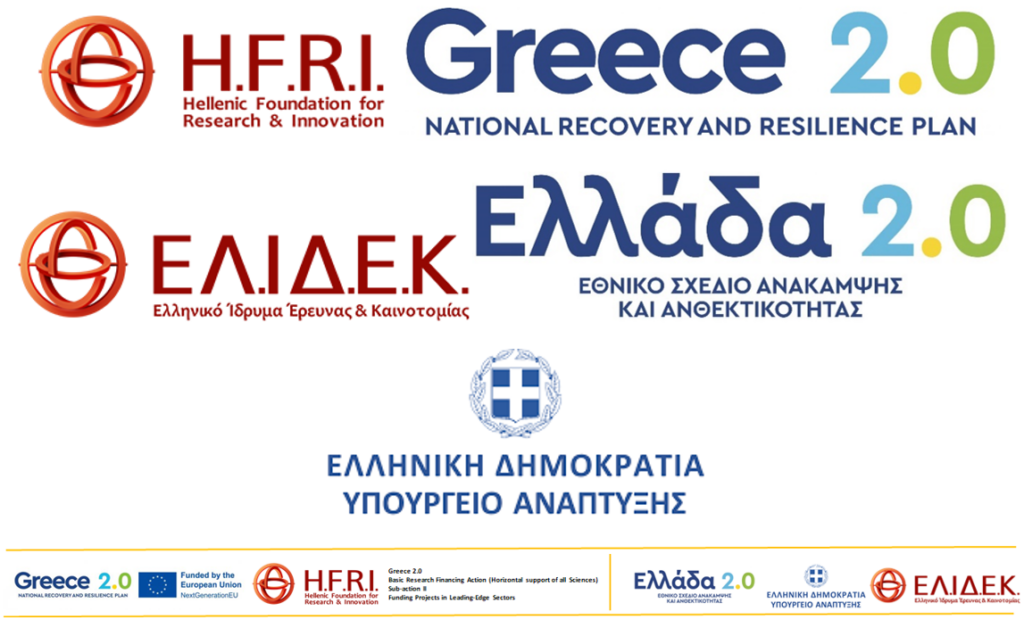
[1] Sun, YC., et al. 4D-printed hybrids with localized shape memory behaviour: Implementation in a functionally graded structure. Sci Rep 9, 18754 (2019). https://doi.org/10.1038/s41598-019-55298-1
[2] Ye Tian, et. al. Recent Progress of Soft Electrothermal Actuators. Soft Robotics. 2021.241-250.http://doi.org/10.1089/soro.2019.0164
[3] Ji, Q., et. al. 4D Thermomechanical metamaterials for soft microrobotics. Commun Mater 2, 93 (2021). https://doi.org/10.1038/s43246-021-00189-0
[4] Qiyi Chen, et. al. 4D Printing via an Unconventional Fused Deposition Modeling Route to High-Performance Thermosets. ACS Appl. Mater. Interfaces 12, 44, 50052–50060 (2020). https://doi.org/10.1021/acsami.0c13976
[5] Andrew Y. Chen et. al. 4D Printing of Electroactive Materials: A review. Adv. Intel. Syst. 2021, 3, 2100019. https://doi.org/10.1002/aisy.202100019
[6] Hiraoka, M., et al. Power-efficient low-temperature woven coiled fibre actuator for wearable applications. Sci Rep 6, 36358 (2016). https://doi.org/10.1038/srep36358https://doi.org/10.1038/srep36358
[7] Hongqiu Wei, et. al. Direct 3D Printing of Hybrid Nanofiber-Based Nanocomposites for Highly Conductive and Shape Memory Applications. ACS Appl. Mater. Interfaces 2019, 11, 27, 24523–24532. https://doi.org/10.1021/acsami.9b04245