THUNDER will develop advanced 3DP structures based on new “soft” polymeric materials towards final 4DP soft ETA devices, through the realization of the following scientific objectives:
O1. To achieve high-quality of nanodispersion in the different polymer matrices via optimum melt-mixing/ compounding processes by a twin screw-extrusion process
O2. To achieve high-quality and printable thermoplastic filaments as feedstock for the 3DP process i.e. with homogeneous diameter (d=1.75 ± 0.5 mm) and shape (fully cylindrical), with/ without conductive nano-inclusions via single-screw extrusion processes: neat polymers and nanocomposite polymer compounds
O3. To obtain a set of optimum 3DP process parameters towards high-quality and efficient 3DP manufacturing with reduced at maximum extent internal and external voids via high degree of inter- and intra-layer fusion, layers interface quality: reach FFF layer thickness of 100µm for both neat polymers, conductive nanocomposite polymers, blend systems and conductive polymer blend systems
O4. To maintain the nanoparticle dispersion upon 3DP filament single-screw extrusion process and 3DP process required for the final 4DP structures
O5. To achieve high interfacial strength in the 3D printed “bi-metallic” like 4DP structures via fusion of the polymer chains between the two different 3DP thermoplastic in nature polymeric layers
O6. To achieve electrical conductivities (σ, S/m) for electrically conductive polymer nanocomposites (needed for the 4DP “Bimetallic-like” stacks/ bi-layer structures) and polymer blend nanocomposites (needed for the “bulk” 4DP ETA devices) above 102 S/m, with the lowest possible nanoparticle solid content and appropriate rheology for 3DP manufacturing
O7. To provide a fundamentalunderstanding of the behavior, and predict the structure, morphology and viscoelastic properties of polymer blends and polymer conductive nanocomposites via computational methodologies across various scales
O8. To control and tailor the thermomechanical properties of materials printed into the final 4DP ETA devices towards the best device performance upon application of Vbias
The overall Research Approach & Methodology of THUNDER project is represented by its corresponding workplan structure, being divided into seven (7) workpackages (WPs). Specifically, the work will be conducted by 4 PhD students, 2 Post-Doctoral Assistant (PDRA), 6 senior investigators being the PIs and co-PIs from the 4 participating entities (collaborative project with 4 entities in the consortium, namely HMU, FORTH, UOP, AUTH), while the PI and Project Coordinator (PCo) from HMU (Assoc. Prof. L. Tzounis) will be involved both in active research and project management.
[WP1] will focus on the Specifications and Definition of Materials, 3D/ 4D Processes & Components. [WP2] will be dedicated to the development of conductive polymer nanocomposites by twin- and single-screw extrusion processes. [WP3] activities will be devoted to 3DP activities of electrothermal polymer nanocomposites. [WP4] is related to all the characterisation activities that will be performed e.g. melt-rheology, DMA, DSC, TGA, Raman, optical- SEM, etc. [WP5] will focus on the modelling activities. [WP6] is related to the 4DP structures as ETA devices and the final multiple U-shape interconnected actuators, control and evaluation of performance. [WP7] is dedicated to the Project Management, Dissemination & Communication activities management.
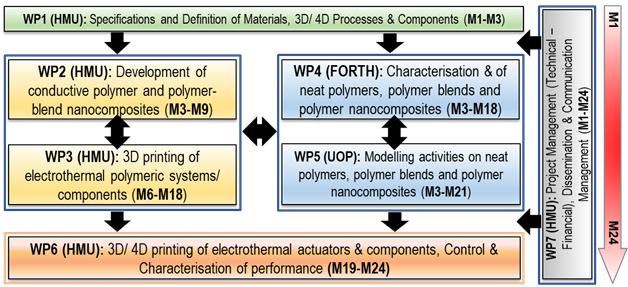